ГОСТ 17053.1-80
Группа Л63
ОКП 25 3212
Срок действия с 01.01.82
до 01.01.87*
________________________________
* Ограничение срока действия снято постановлением
Госстандарта СССР от 26.12.91 N 2166 (ИУС N 4, 1992 год). -
Примечание изготовителя базы данных.
РАЗРАБОТАН Министерством нефтеперерабатывающей и нефтехимической промышленности СССР
ИСПОЛНИТЕЛИ
Б.М.Горелик, А.А.Шляхман, М.А.Закирова, Л.Н.Лысенкова, Е.Д.Субботникова, И.Е.Новоселова, Т.В.Лабутина
ВНЕСЕН Министерством нефтеперерабатывающей и нефтехимической промышленности СССР
Член Коллегии А.И.Лукашов
УТВЕРЖДЕН И ВВЕДЕН В ДЕЙСТВИЕ Постановлением Государственного комитета СССР по стандартам от 30 мая 1980 г. N 2446
ВЗАМЕН ГОСТ 17053-71 в части разд.1-6 для амортизаторов
ВНЕСЕНЫ: Изменение N 1, утвержденное и введенное в действие Постановлением Государственного комитета СССР по стандартам от 30.06.83 N 2793 с 01.01.84, Изменение N 2, утвержденное и введенное в действие Постановлением Государственного комитета СССР по стандартам от 24.12.86 N 4493 с 01.06.87, Изменение N 3, утвержденное и введенное в действие Постановлением Комитета стандартизации и метрологии СССР от 26.12.91 N 2166 с 01.08.92
Изменения N 1, 2, 3 внесены изготовителем базы данных по тексту ИУС N 10, 1983 год, ИУС N 4, 1987 год, ИУС N 4, 1992 год
Настоящий стандарт распространяется на резинометаллические корабельные сварные со страховкой маслостойкие амортизаторы АКСС-М, предназначенные для виброизоляции и защиты от ударных воздействий оборудования на судах.
Амортизаторы предназначены для работы в воздушной среде в присутствии паров масла и дизельного топлива, а также при возможном попадании масла, дизельного топлива, пресной и морской воды при температуре от минус 10 до плюс 70 °С, кратковременно (не более 1 ч и не чаще одного раза в месяц) от минус 10 до плюс 100 °С, а также при температуре до минус 40 °С в нерабочем состоянии (без нагрузки) в период достройки судов под амортизируемым оборудованием.
Амортизаторы предназначены для работы в вибрационном режиме с частотой до 50 Гц с амплитудами деформирования резинового массива в направлении осей
,
,
до 0,2 мм.
Амортизаторы АКСС-М могут применяться для амортизации механизмов, приборов, агрегатов в других отраслях народного хозяйства.
Настоящий стандарт устанавливает требования к корабельным амортизаторам АКСС-М, изготовленным для нужд народного хозяйства и для поставки на экспорт.
Требования настоящего стандарта, кроме пп.2.2, 2,5, 2.7, являются обязательными.
(Измененная редакция, Изм. N 1, 2, 3).
1. ТИПЫ, ОСНОВНЫЕ ПАРАМЕТРЫ И РАЗМЕРЫ
1.1. В зависимости от конструкции арматуры амортизаторы должны изготовляться следующих типов:
бескозырьковый - на нагрузки 98-1177 Н (10-120 кгс);
козырьковый - на нагрузки 1570-3924 Н (160-400 кгс).
1.2. Конструкция, основные параметры и размеры амортизаторов должны соответствовать указанным на черт.1, 2 и в табл.1. Неуказанные размеры и предельные отклонения должны соответствовать чертежам, согласованным в установленном порядке.
Черт.1. Бескозырьковый амортизатор
Бескозырьковый амортизатор
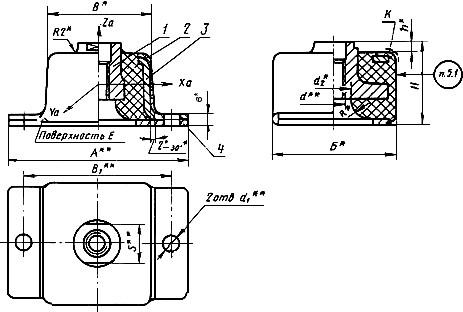
1 - несущая планка; 2 - резиновый массив; 3 - скоба; 4 - опорная планка
Черт.1*
_________________
* Черт.1. Измененная редакция, Изм. N 1.
Черт.2. Козырьковый амортизатор
Козырьковый амортизатор
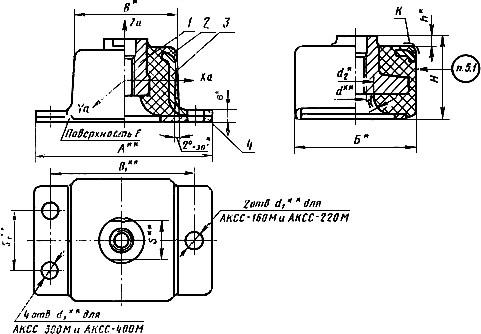
1 - несущая планка; 2 - резиновый массив; 3 - скоба; 4 - опорная планка
Черт.2*
_________________
* Черт.2. Измененная редакция, Изм. N 1.
Таблица 1
Размеры в мм
| | | **
| *
| *
| 
| 
| 
| 
| 
| 
| 
| 
| 
| 
| | |
Обозна- чение аморти- затора | Тип аморти- затора | Максима- льная рабочая нагруз- ка по оси Za, Н (кгс) | | Пред. откл, +2,0
| Пред. откл, ±0,5
| Но- мин. | Пред. откл.
| Пред. откл. +1,5
| | Пред. откл. по Н14 | Пред. откл. по 17
| | | | Но- мин. | Пред. откл. | Пред. откл. по 17 | Груп- па рези- ны | Масса 1 шт. (спра- воч- ная), кг |
АКСС-10М, АКСС-10М-1
| Беско- зырь- ковый | 98(10) | 70 | 43 | 40 | 54 | ±0,2 | 5 | М8-7Н | 7 | 15 | 14 | - | 10 | 40 | +2,0 -0,5 | 6 | 1 | 0,19 |
АКСС-15М, АКСС-15М-1
| | 147(15) | | 48 | | | | 6 | | | | | | | | | | | 0,23 |
АКСС-25М, АКСС-25М-1
| | 245(25) | | | | | | | | | | | | | | | | 2 | |
АКСС-40М, АКСС-40М-1
| | 392(40) | 85 | 63 | 48 | 68 | | | М10-7Н | 9 | 18 | 17 | | 12 | 46 | | 7 | | 0,44 |
АКСС-60М, АКСС-60М-1
| | 589(60) | 100 | 73 | 56 | 80 | | 8 | М12-7Н | | 22 | 22 | | | 50 | | 8 | | 0,75 |
АКСС-85М, АКСС-85М-1
| | 834(85) | 120 | 80 | 76 | 100 | | | М14-7Н | 11 | 24 | 27 | | 17 | 60 | | 9 | | 1,15 |
АКСС-120М, АКСС-120М-1
| | 1177(120) | 140 | 95 | 80 | 112 | ±0,3 | | М16-7Н | 13 | 25 | 32 | | 20 | 65 | | | | 1,60 |
АКСС-160М, АКСС-160М-1
| Козырь- ковый | 1570(160) | 145 | 108 | 81 | 115 | | 12 | М18-7Н | | 28 | | | 11 | 60 | +2,5 -0,5 | 11 | | 2,00 |
АКСС-220М, АКСС-220М-1
| | 2158(220) | 150 | 118 | 86 | 120 | | | М22-7Н | 15 | 30 | 36 | | 10 | | | 9 | 3 | 2,50 |
АКСС-300М, АКСС-300М-1
| | 2943(300) | 155 | 125 | 88 | 125 | | 13 | М24-7Н | | 32 | 41 | 60 | 12 | 65 | | 11 | | 3,00 |
АКСС-400М, АКСС-400М-1
| | 3924(400) | 175 | 130 | 96 | 140 | | | М27-7Н | 17 | 35 | 44 | 65 | 11 | | | 9 | | 3,30 |
Примечания:
1. Размеры, обозначенные знаком "**", являются справочными.
2. Размеры, обозначенные знаком "*", являются исполнительными и обеспечиваются инструментом.
3. Данные по применению амортизаторов указаны в справочном приложении.
Пример условного обозначения амортизаторов на нагрузку 245 Н с арматурой из стали обыкновенного качества, предназначенных для районов с умеренным климатом:
АКСС-25М ГОСТ 17053.1-80
То же, из высоколегированной стали:
АКСС-25М-1 ГОСТ 17053.1-80
Пример условного обозначения амортизаторов на нагрузку 245 Н с арматурой из стали обыкновенного качества, предназначенных для районов с тропическим климатом:
АКСС-25М-Т ГОСТ 17053.1-80
То же, из высоколегированной стали:
АКСС-25М-1-Т ГОСТ 17053.1-80
(Измененная редакция, Изм. N 1).
2. ТЕХНИЧЕСКИЕ ТРЕБОВАНИЯ
2.1. Амортизаторы должны изготовляться в соответствии с требованиями настоящего стандарта по технической документации, утвержденной в установленном порядке.
2.2. Физико-механические показатели резиновых смесей должны быть указаны в нормативно-технической документации.
(Измененная редакция, Изм. N 2).
2.3. Арматура, применяемая для изготовления амортизаторов, должна соответствовать требованиям ГОСТ 17053.2-80.
2.4. Резиновый массив амортизаторов в местах разреза не должен иметь расслоений, пор и посторонних включений, видимых невооруженным глазом.
2.5. На поверхности амортизаторов допускаются:
местные оголения металла ребер опорной планки;
отслоения резиновой пленки от ребер опорной планки;
заплывы резины на внешнюю неопорную поверхность арматуры;
коррозионный налет на необрезиниваемых поверхностях металларматуры.
При необходимости перед монтажом изделий удаляют коррозионный налет с сохранением размеров амортизаторов в пределах допусков и затем наносят защитное лакокрасочное покрытие на необрезиниваемые поверхности амортизаторов.
(Измененная редакция, Изм. N 3).
2.6. На поверхности резинового массива амортизаторов не допускаются пузыри, раковины, обрывы, отслоения резины от арматуры, трещины на закруглениях резинового массива в местах его контакта со скобой и опорной планкой (поверхность Е), а также отклонения, превышающие указанные в табл.3.
Таблица 3*
___________
* Таблица 2.
Исключена Изм. N 2.
| Наименование отклонения | Размер отклонения, не более
|
1 | Недопрессовки:
| |
| глубиной, мм
| 0,5 |
| общей площадью, мм
| 30 |
2 | Втянутые кромки по месту разъема пресс-формы, мм:
| |
| глубиной
| 2,0 |
| шириной
| 3,0 |
3. | Следы облоя по периметру, мм:
| |
| толщиной
| 1,0 |
| высотой
| 2,0 |
4. | Смещение резинового массива по месту разъема пресс-формы, мм
| 1,0 |
5. | Возвышения и углубления:
| |
| высотой, мм
| 1,0 |
| глубиной, мм
| 1,0 |
| общей площадью, мм
| 30 |
6. | 6. Следы облоя по месту разъема пресс-формы в виде "гребешка", мм:
| |
| высотой
| 2,0 |
| толщиной
| 2,0 |
7. | Заплывы резины:
| |
| на опорную поверхность толщиной, мм
| 1,0 |
| на нижнюю часть резьбы несущей планки
| Два витка |
| на внешнюю поверхность металлической арматуры, мм
| 1,0 |
8. | Прослойка резины между деталями 3 и 4 толщиной, мм
| 1,0 |
9. | Остатки литников в нижней части несущей планки высотой, мм
| Выступающие за плоскость опорной планки |
10. | Искажение формы резинового массива на сторону
| Глубиной 1,0 мм |
(Измененная редакция, Изм. N 1, 2).
2.7. Допускается внешний вид амортизаторов устанавливать по контрольному образцу.
2.8. Амортизаторы должны быть работоспособными в условиях сухого и влажного тропического климата и соответствовать группе III категории 2 по ГОСТ 15152-69.
(Измененная редакция, Изм. N 1).
2.9. Амортизаторы должны быть покрыты искусственным воском в соответствии с технической документацией, утвержденной в установленном порядке.
2.10. Деформация амортизаторов при статическом сжатии под воздействием максимальной рабочей нагрузки вдоль оси
должна соответствовать нормам, указанным в табл.4.
Таблица 4
Обозначение амортизатора | Максимальная рабочая нагрузка, Н (кгс)
| Деформация, мм (Пред. откл. ±0,25)
|
АКСС-10М, АКСС-10М-1 | 98 (10)
| 0,6
|
АКСС-15М, АКСС-15М-1
| 147 (15)
| 0,7 |
АКСС-25М, АКСС-25М-1
| 245 (25)
| |
АКСС-40М, АКСС-40М-1
| 392 (40)
| |
АКСС-60М, АКСС-60М-1
| 589 (60) | |
АКСС-85М, АКСС-85М-1 | 834 (85)
| 0,6
|
АКСС-120М, АКСС-120М-1
| 1177 (120)
| 0,9 |
АКСС-160М, АКСС-160М-1
| 1570 (160)
| 0,6 |
АКСС-220М, АКСС-220М-1
| 2158 (220)
| |
АКСС-300М, АКСС-300М-1
| 2943 (300) | |
АКСС-400М, АКСС-400М-1
| 3924 (400) | 0,7 |
Примечание. Деформация уточняется до 01.10.92.
(Измененная редакция, Изм. N 3).
2.11. Амортизаторы должны выдерживать предельную статическую нагрузку вдоль оси
, указанную в табл.5.
Таблица 5
Обозначение амортизатора | Статическая нагрузка, Н(кгс), не менее
|
АКСС-10М, АКСС-10М-1
| 1472 (150) |
АКСС-15М, АКСС-15М-1
| 2207 (225) |
АКСС-25М, АКСС-25М-1
| 3679 (375) |
АКСС-40М, АКСС-40М-1
| 5886 (600) |
АКСС-60М, АКСС-60М-1
| 8829 (900) |
АКСС-85М, АКСС-85М-1
| 12508 (1275) |
АКС-120М, АКСС-120М-1
| 17658 (1800) |
АКСС-160М, АКСС-160М-1
| 23544 (2400) |
АКСС-220М, АКСС-220М-1
| 32373 (3300) |
АКСС-300М, АКСС-300М-1
| 44745 (4500) |
АКСС-400М, АКСС-400М-1
| 58860 (6000) |
(Измененная редакция, Изм. N 2).
3. ПРАВИЛА ПРИЕМКИ
3.1. Амортизаторы принимают партиями. Партией считают амортизаторы одного типоразмера, изготовленные из одной группы резины, в количестве не более 1000 шт, сопровождаемые одним документом о качестве. Документ о качестве должен содержать следующие данные:
условное обозначение амортизатора;
номер партии;
количество мест в партии;
наименование и товарный знак предприятия-изготовителя или товарный знак;
дату изготовления (квартал и год);
результаты проведенных испытаний и подтверждение о соответствии требованиям настоящего стандарта.
(Измененная редакция, Изм. N 1).
3.2. Для проверки качества амортизаторов требованиям настоящего стандарта амортизаторы подвергаются приемо-сдаточным, периодическим и типовым испытаниям в соответствии с табл.6.
Таблица 6
Наименование показателя | Объем выборки и периодичность испытания | Вид испытания
|
|
| приемо- сдаточные
| периоди- ческие | типовые |
1. Внешний вид амортизаторов
| Все амортизаторы партии | + | - | + |
2. Расслоение, поры и посторонние включения
| 3 шт. от партии | + | - | + |
3. Высота амортизаторов
| Все амортизаторы партии
| + | - | + |
4. Исполнительные размеры амортизаторов | Не менее 2 шт. с каждого гнезда пресс-формы
| - | + | + |
5. Деформация амортизаторов вдоль оси при статическом сжатии
| 2% от партии, но не менее 3 шт. | + | - | + |
6. Предельная статическая нагрузка
| 1% от партия, но не менее 3 шт. | + | - | + |
7. Физико-механические показатели резины
| Не реже двух раз в месяц от текущей закладки
| - | + | + |
Примечания:
1. Знак "+" обозначает проведение испытаний, знак "-" - отсутствие испытаний.
2. Проверку по подпункту 4 таблицы проводят при вводе в эксплуатацию новых и отремонтированных пресс-форм.
3. Амортизаторы, прошедшие испытания на предельную статическую нагрузку, к использованию по назначению непригодны.
3.3. Потребитель проводит входной контроль качества амортизаторов по плану, принятому для приемо-сдаточных испытаний, в количестве 1,0% от партии, но не менее 3 шт.
3.4. При получении неудовлетворительных результатов приемо-сдаточных испытаний хотя бы по одному из показателей по подпунктам 2, 5 и 6 табл.6 по нему проводят повторные испытания на удвоенном объеме выборки, взятой от той же партии.
Результаты повторных испытаний по подпунктам 2 и 6 распространяются на всю партию.
При получении неудовлетворительных результатов повторных испытаний по подпункту 5 табл.6 партию амортизаторов подвергают сплошному контролю.
3.5. При получении неудовлетворительных результатов периодических испытаний по подпункту 4 табл.6 проводят повторные испытания на удвоенном количестве амортизаторов, взятых от тех же пресс-форм.
При получении неудовлетворительных результатов испытания переводят в приемо-сдаточные до получения положительных результатов.
3.6. При получении неудовлетворительных результатов испытаний хотя бы по одному из показателей по подпункту 7 табл.6 проводят повторные испытания по этому показателю на удвоенном объеме выборки, взятой от той же закладки резиновой смеси.
При получении неудовлетворительных результатов повторных испытаний проводят испытания по этому показателю до получения положительных результатов на всех закладках суточной выработки.
(Измененная редакция, Изм. N 2).
4. МЕТОДЫ ИСПЫТАНИЙ
4.1. Амортизаторы испытывают не ранее, чем через 16 ч после их изготовления, но не позднее, чем через 60 сут.
Перед испытанием амортизаторы выдерживают при температуре испытания не менее 3 ч.
(Измененная редакция, Изм. N 2).
4.2. Внешний вид амортизаторов проверяют визуально или сравнением с контрольным образцом.
4.3. Проверку амортизаторов на отсутствие в резиновом массиве расслоений, пор и посторонних включений проводят визуальным контролем мест разреза, нанесенных в различных направлениях. Для проверки можно использовать амортизаторы, имеющие отклонения по внешнему виду или прошедшие испытания на статическую прочность, а также изготовленные без арматуры.
4.4. Размеры амортизаторов определяют штангенциркулем или универсальным инструментом, обеспечивающим погрешность измерения не более 0,1 мм.
4.3, 4.4. (Измененная редакция, Изм. N 2).
4.5. Деформацию амортизаторов при статическом сжатии под воздействием максимальной рабочей нагрузки определяют при температуре (23±2) °С. Амортизатор устанавливают в центре нижней плиты пресса или реверсера. Сближая сжимающие поверхности со скоростью 10-15 мм/мин, доводят нагрузку на амортизатор до указанной в табл.4. Амортизаторы нагружают два раза подряд с интервалом не более 10 с. Затем выдерживают без нагрузки не менее (60±15) с, после чего сближают плиты пресса или реверсера до соприкосновения верхней плиты с несущей планкой амортизатора и при достижении нагрузки, равной 5% максимальной, стрелку индикатора, измеряющего деформацию, устанавливают на нуль. Продолжают нагружать амортизатор до нагрузки, указанной в табл.4, и считают показания индикатора, которые соответствуют деформации сжатия. Измерение производят с погрешностью не более 0,01 мм.
4.6. Предельную статическую нагрузку определяют при 23±2 °С. Амортизатор нижней опорной плоскостью устанавливают в центре нижней плиты или реверсера.
Сближением сжимающих поверхностей со скоростью 10-15 мм/мин доводят нагрузку до величины, указанной в табл.5. Нагрузку выдерживают в течение 1 мин и проверяют амортизатор на отсутствие отслоения резины от металла, трещин и других повреждений после снятия нагрузки.
4.5, 4.6. (Измененная редакция, Изм. N 3).
5. МАРКИРОВКА, УПАКОВКА, ТРАНСПОРТИРОВАНИЕ И ХРАНЕНИЕ
5.1. На боковой поверхности резинового массива амортизатора оттиском от пресс-формы наносят маркировку с указанием:
товарного знака предприятия-изготовителя;
условного обозначения амортизатора;
двух последних цифр года изготовления амортизатора.
Места маркировки должны соответствовать указанным на черт.1 и 2. Штамп отдела технического контроля и квартал изготовления наносят несмываемой водой краской.
Допускается в условном обозначении амортизатора АКСС-10М-АКСС-40М не указывать обозначение настоящего стандарта.
Дополнительно маркировку года допускается производить точками, сумма которых с указанной цифрой года обозначает год изготовления.
Допускается использовать имеющийся парк пресс-форм с маркировкой по ранее действующей документации до полного износа.
Амортизаторы АКСС-М, предназначенные для эксплуатации в условиях тропическою климата, дополнительно маркируют желтой краской в соответствии с ГОСТ 15152-69, разд.8 или проставляют маркировку на ярлыке.
(Измененная редакция, Изм. N 1, 2).
5.2. Амортизаторы одного типоразмера упаковывают в деревянные ящики по ГОСТ 16511-77* и ГОСТ 16536-84**, выложенные внутри бумагой по ГОСТ 8273-75.
_______________
* На территории Российской Федерации действует ГОСТ 16511-86.
** На территории Российской Федерации действует ГОСТ 16536-90. - Примечание изготовителя базы данных.
По согласованию между изготовителем и потребителем допускается использовать бумаги и ящики, не предусмотренные настоящим стандартом, при транспортировании транспортом всех видов, кроме речного, и упаковывать в один ящик амортизаторы разных типоразмеров и партий при условии их раздельного упаковывания внутри ящика. Масса брутто одной упаковки не более 50 кг.
Допускается по согласованию между потребителем и изготовителем упаковывание амортизаторов в контейнеры.
(Измененная редакция, Изм. N 2, 3).
5.3. Транспортную тару маркируют по ГОСТ 14192-77* с дополнительным указанием на ярлыке:
_______________
* На территории Российской Федерации действует ГОСТ 14192-96. - Примечание изготовителя базы данных.
наименования детали;
количества деталей;
обозначения настоящего стандарта.
5.4. Амортизаторы транспортируют всеми видами транспорта в крытых транспортных средствах в соответствии с правилами перевозки грузов, действующими на транспорте данного вида.
(Измененная редакция, Изм. N 2).
5.5. Амортизаторы должны храниться в ящиках в закрытом помещении при температуре не выше 25 °С на расстоянии не менее 1 м от теплоизлучающих приборов.
Допускается хранение амортизаторов в неотапливаемых складах при температуре до минус 40 °С.
Перед использованием после хранения при температуре ниже 0 °С амортизаторы должны быть выдержаны без деформации при температуре 23±2 °С не менее 24 ч.
6. ГАРАНТИИ ИЗГОТОВИТЕЛЯ
6.1. Изготовитель гарантирует соответствие амортизаторов требованиям настоящего стандарта при соблюдении условий транспортирования и хранения.
6.2. Гарантийный срок хранения амортизаторов - 3 года со дня изготовления.
6.3. Гарантийный срок эксплуатации амортизаторов - 10 лет со дня ввода их в эксплуатацию.
6.2, 6.3. (Измененная редакция, Изм. N 2).
6.4. Допускается увеличение гарантийного срока хранения амортизаторов при соответствующем уменьшении гарантийного срока эксплуатации.
6.5. К концу гарантийного срока эксплуатации и хранения допускается уменьшение значений показателей:
статической деформации - до 50% от исходной;
статической прочности - в три раза, что обеспечивает сохранение целостности изделия при двухкратном ударном деформировании на величину свободного хода;
высоты изделия - до 10% от величины свободного хода.
(Введен дополнительно, Изм. N 2).
ПРИЛОЖЕНИЕ (справочное). ДАННЫЕ ПО ПРИМЕНЕНИЮ АМОРТИЗАТОРОВ АКСС-М
ПРИЛОЖЕНИЕ
Справочное
1. Статические, динамические (вибрационные) и динамические ударные жесткости в направлении осей
,
,
амортизаторов АКСС-М указаны в табл.1.
Таблица 1
Обозна- чение аморти- затора | Максимальная рабочая нагрузка, Н (кгс) | Статическая жесткость, кН/м (кгс/см), соответствующая деформации | Динамическая (вибрационная) жесткость, кН/м (кгс/см), соответствующая деформации
| Ударная жесткость, кН/м (кгс/см), соответствующая деформации | Значение свободного хода амортизатора по осям , , , мм |
| в направлении осей , и амортизатора | |
| 
| 
| 
| 
| 
| 
| 
| 
| 
| 
| 
| 
|
|
|
|
АКСС-10М
| 98(10) | 98(10) | 49(5) | 122,5(125) | 166,6(170) | 98(100) | 539(550) | 784(800) | 294(300) | 588(600) | 1669(1700) | 490(500) | 7 | 7 | 8 |
АКСС-15М
| 147(15) | 147(15) | 98(10) | 147(150) | 245(250) | 127,4(130) | 637(650) | 1127(1150) | 441(450) | 686(700) | 2450(2500) | 735(750) | 7 | 7 | 8 |
АКСС-25М
| 245(25) | 245(25) | 98(10) | 215,6(220) | 490(500) | 205,8(210) | 1078(1100) | 1176(1200) | 637(650) | 1176(1200) | 2548(2600) | 1568(1600) | 7 | 7 | 8 |
АКСС-40М
| 392(40) | 392(40) | 147(15) | 392(400) | 588(600) | 343(350) | 1617(1650) | 1666(1700) | 980(1000) | 1862(1900) | 3822(3900) | 1666(1700) | 9 | 9 | 10 |
AКCC-60M
| 588(60) | 588(60) | 245(25) | 627,2(640) | 784(800) | 588(600) | 2156(2200) | 1666(1700) | 882(900) | 2744(2800) | 3920(4000) | 1862(1900) | 10 | 10 | 10 |
AКCC-85M
| 833(85) | 833(85) | 343(35) | 833(850) | 882(900) | 607,6(620) | 3038(3100) | 1862(1900) | 980(1000) | 3920(4000) | 4802(4900) | 2058(2100) | 9 | 9 | 11 |
АКСС-120М
| 1176(120) | 1078(110) | 490(50) | 1127(1150) | 1176(1200) | 637(650) | 3430(3500) | 2058(2100) | 1274(1300) | 4410(4500) | 5292(5400) | 2450(2500) | 12 | 12 | 12 |
АКСС-160М
| 1568(160) | 1470(150) | 686(70) | 2744(2800) | 1568(1600) | 686(700) | 7448(7600) | 2254(2300) | 1568(1600) | 9800(10000) | 5880(6000) | 3136(3200) | 11 | 11 | 12 |
АКСС-220М
| 2156(220) | 1862(190) | 784(80) | 4606(4700) | 2450(2500) | 735(750) | 9800(10000) | 2940(3000) | 2744(2800) | 19600(20000) | 10584(10800) | 7448(7600) | 10 | 10 | 12 |
АКСС-300М
| 2940(300) | 2058(210) | 882(90) | 5096(5200) | 3136(3200) | 784(800) | 1079(11000) | 4116(4200) | 1960(2000) | 19600(20000) | 7448(7600) | 5390(5500) | 10 | 10 | 12 |
АКСС-400М
| 3920(400) | 2548(260) | 980(100) | 7056(7200) | 3920(4000) | 882(900) | 14210(14500) | 5488(5600) | 2548(2600) | 29400(30000) | 11368(11600) | 7840(8000) | 10 | 10 | 12 |
Примечания:
1. Динамические (вибрационные) жесткости указаны для амортизаторов, деформируемых с амплитудами от 0,2 до 1,0 мм при частотах от 200 до 3000 колебаний в 1 мин и температуре 15-20 °С.
2. Ударные жесткости указаны для амортизаторов, деформируемых при температуре 15-20 °С со скоростью от 1 до 6 м/с.
3. После пребывания амортизаторов в течение 1 ч и более при температуре минус 10 °С ударные жесткости, указанные в таблице, повышаются:
- в 3,0-5,0 раз;
- в 1,5-2,0 раза;
- в 2,0-2,5 раза.
При температуре 60 °С ударные жесткости (
и
), приведенные в таблице, уменьшаются:
- на 40-75%;
- на 20%.
Ударные жесткости
остаются без изменений, а динамические (вибрационные) уменьшаются на 20-30
4. Коэффициент демпфирования составляет в среднем 0,20-0,25.
5. Свободный ход амортизатора - предельная деформация, ограниченная конструкцией (прочностью) амортизатора при его статическом (динамическом) нагружении.
(Измененная редакция, Изм. N 2).
2. Амортизаторы АКСС-М для амортизации оборудования на горизонтальной плоскости выбирают в соответствии со схемами 1-9 (черт.1) и табл.2.
При креплении оборудования к вертикальной плоскости допускается установка амортизаторов по схемам 7-9.
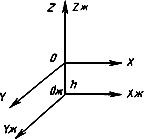
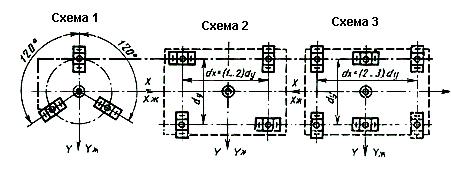
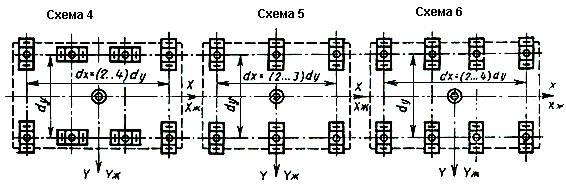
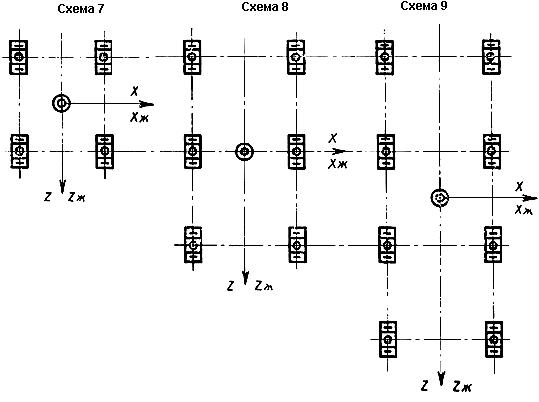
Условные обозначения:
,
,
- главные центральные оcи инерции амортизируемого оборудования;
,
,
- главные центральные оси жесткости амортизируемого крепления;
- центр тяжести амортизируемого объекта;
- центр жесткости амортизируемого крепления;
- расстояние между центром тяжести и центрам жесткости или плоскостью размещения амортизаторов.
Черт.1
Таблица 2
| | Масса амортизируемого объекта при его установке, кг
| | Масса амортизируемого объекта при его установке, кг |
Обозна- чение аморти- затора | Рекомендуемая нагрузка на один амортизатор, Н (кгс)
| на три аморти- затора (схема 1)
| на четыре аморти- затора (схемы 2 и 7)
| на шесть аморти- заторов (схемы 3, 5 и 8) | на восемь аморти- заторов (схемы 4, 6 и 9)
| Рекомендуемая нагрузка на один амортизатор, Н (кгс) | на три аморти- затора (схема 1) | на четыре аморти- затора (схемы 2 и 7) | на шесть аморти- заторов (схемы 3, 5 и 8)
| на восемь аморти- заторов (схемы 4, 6 и 9)
|
| Для 600 при 
500 при 
300 при 
| Для 500< <600 при 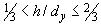
300< <500 при |
АКСС-10М
| 49-98(5-10) | 15-30 | 20-40 | 30-60 | 40-80 | 49-98(5-10) | 15-30 | 20-40 | 30-60 | 40-80 |
АКСС-15М
| 98-147(10-15) | 30-45 | 40-60 | 60-90 | 80-120 | 98-147(10-15) | 30-45 | 40-60 | 60-90 | 80-120 |
АКСС-25М
| 147-245(15-25) | 45-75 | 60-100 | 90-150 | 120-200 | 147-245(15-25) | 45-75 | 60-100 | 90-150 | 120-200 |
АКСС-40М
| 245-392(25-40) | 75-120 | 100-160 | 150-240 | 200-320 | 245-392(25-40) | 75-120 | 100-160 | 150-240 | 200-320 |
АКСС-60М
| 392-588(40-60) | 120-180 | 160-240 | 240-360 | 320-480 | 392-588(40-60) | 120-180 | 160-240 | 240-360 | 320-480 |
АКСС-85М | 588-833(60-85) | 180-250 | 240-340 | 360-500 | 480-680 | 588-833(60-85)
| 180-250 | 240-340 | 360-500 | 480-680 |
АКСС-120М
| 833-1176(85-120) | 250-360 | 340-480 | 500-720 | 680-960 | 833-980(85-100) | 250-300 | 340-400 | 500-600 | 680-800 |
АКСС-160М
| 1176-1569(120-160) | 360-480 | 480-640 | 720-960 | 960-1300 | 980-1568(100-160) | 300-480 | 400-640 | 600-960 | 800-1300 |
АКСС-220М
| 1568-2156(160-220) | 480-660 | 640-880 | 960-1300 | 1300-1760 | 1568-2156(160-220) | 480-660 | 640-880 | 960-1300 | 1300-1760 |
АКСС-300М
| 2156-2940(220-300) | 660-900 | 880-1200 | 1300-1800 | 1760-2400 | 2656-2744(220-280) | 660-850 | 880-1100 | 1300-1700 | 1760-2200 |
АКСС-400М
| 2940-3920(300-400) | 900-1200 | 1200-1600 | 1800-2400 | 2400-3200 | 2744-3528(280-360)
| 850-1000 | 1100-1500 | 1700-2200 | 2200-2900 |
Примечания:
1. При несоблюдении указанных в таблице соотношений
для выбора амортизаторов производить расчет.
2.
- наибольшее число оборотов в минуту.
3.
,
- по рекомендуемым схемам расположения амортизаторов.
3. Амортизаторы под приборы, аппараты, щиты и вспомогательные механизмы, не имеющие неуравновешенных сил и моментов, выбирают по табл.2 в следующем порядке.
Определяют по наибольшему числу оборотов и по соотношению
часть таблицы, по которой должны быть выбраны амортизаторы. Выбирают по числу крепежных отверстий амортизируемого объекта схему размещения амортизаторов в амортизирующем креплении.
Находят по массе амортизируемого объекта обозначение амортизатора. Если масса амортизируемого объекта не позволяет подобрать количество амортизаторов по числу крепежных отверстий, следует применять переходные конструкции. В этом случае при выборе амортизаторов масса агрегата и его высота должны приниматься с учетом переходных конструкций.
4. При монтаже амортизирующего крепления должны соблюдаться следующие требования:
установку амортизаторов допускается производить при температуре окружающей среды не ниже минус 10 °С;
необходимо соблюдать установленные зазоры между корпусом и рамой амортизируемого объекта и окружающими его твердыми предметами, а также соседними амортизируемыми объектами;
при монтаже амортизирующего крепления с расположением амортизаторов в различных плоскостях первоначально должны монтироваться опорные амортизаторы, воспринимающие нагрузку от массы амортизируемого объекта.
Амортизаторы, располагаемые в других плоскостях (упорные амортизаторы), должны монтироваться не ранее, чем через 2 сут после монтажа опорных амортизаторов.
Монтаж упорных амортизаторов можно производить сразу после установки объекта на опорные амортизаторы при условии, что опорные амортизаторы будут выдержаны под максимальной рабочей нагрузкой не менее 2 сут;
при монтаже амортизирующих креплений объектов, устанавливаемых на вертикальных и наклонных фундаментах, перекос плоскости крепления объекта к амортизаторам по отношению к плоскости фундамента не должен превышать 3 мм на 1 м;
амортизаторы должны плотно без качаний, прилегать к плоскости фундамента (черт.2);
для устранения зазоров между торцовыми опорными поверхностями хвостовиков несущих планок амортизаторов и опорными поверхностями амортизируемого объекта (разности по высоте между отдельными амортизаторами амортизирующего крепления) должны применяться стальные выравнивающие шайбы диаметром, равным не менее двух диаметров крепежных болтов или шпилек и толщиной от 3 до 20 мм.
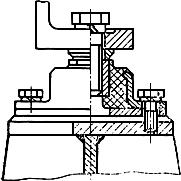
Черт.2
Выравнивающие шайбы изготовляют по 5-му классу точности; шероховатость нижней и верхней поверхностей после обработки выравнивающих шайб
не должна превышать 20 мкм. Острые кромки шайб должны быть запилены;
при определении толщин выравнивающих шайб амортизируемый объект следует установить без перекосов на жестких опорах и замерить с погрешностью не более 0,1 мм зазоры между опорными торцовыми поверхностями несущих втулок амортизаторов и опорной поверхностью амортизируемого объекта.
Если разность между наибольшим и наименьшим зазором не более 0,3 мм, то объект допускается устанавливать непосредственно на амортизаторы, если более 0,3 мм - объект устанавливают с применением выравнивающих шайб.
Болт крепления амортизируемого объекта к амортизатору не должен доходить до опорной планки амортизатора.
5. Трубопроводы, водопроводы и кабели, подводимые к амортизируемым механизмам, должны монтироваться не ранее, чем через 2 сут после монтажа опорных амортизаторов.
6. Окраска амортизаторов не допускается.