ГОСТ 17731-79*
Группа Л27
ОКП 22 5319 3000
Дата введения 1980-07-01
Постановлением Государственного комитета СССР по стандартам от 7 августа 1979 г. N 2998 срок действия установлен с 01.07.1980 г.
* ПЕРЕИЗДАНИЕ, август 1998 г., с Изменениями N 1, 2, постановления от 15.03.85 N 601, от 27.11.89 N 3465 (ИУС 6-90)
Настоящий стандарт распространяется на материал П-5-7 ЛДП, изготовленный на основе фенолоформальдегидного связующего и кремнеземных лент или ткани.
Материал предназначается для изготовления деталей, работающих кратковременно в условиях высоких температур.
Материал перерабатывается методом намотки с последующей термообработкой под давлением.
(Измененная редакция, Изм. N 2).
1. ТЕХНИЧЕСКИЕ ТРЕБОВАНИЯ
1.1. Материал должен изготовляться в соответствии с требованиями настоящего стандарта по технологическому регламенту, утвержденному в установленном порядке.
1.2. Материал должен изготовляться в виде пропитанной связующим непрерывной тканой ленты или ткани, марки и размеры которых указаны в табл.1.
Таблица 1
Вид материала
| Марка наполнителя | Размеры | Код ОКП
|
|
| Ширина, мм | Длина, м, не менее
|
|
Лента
| КЛ-11-5,0
| 50±2 | На катушке - 200 | 22 5319 3001 02 |
| КЛ-11-8,2
| 82±4 | | 22 5319 3002 01 |
| КЛ-11-9,4
| 94±4 | | 22 5319 3003 00 |
Ткань
| КЛ-11-ТО, КЛ-11-ТОА, аппретированная раствором продукта АГМ-9
| 800±30 | В рулоне - 45 | 22 5319 3004 10 |
Примечание. Ткань марки КТ-11-ТОА, аппретированную раствором продукта АГМ-9, применяют по согласованию с потребителем.
По согласованию с потребителем допускается уменьшать длину ленты на катушке и ткани в рулоне.
(Измененная редакция, Изм. N 1, 2).
1.3. Длина кусков, склеиваемых любой капроновой тканью (капроновая нить по основе и утку, масса 1 м
ткани - 13-50 г) или сшиваемых кремнеземной нитью, должна быть не менее 10 м.
1.4. По внешнему виду материал должен соответствовать следующим требованиям:
а) цвет от светло- до темно-желтого, желто-зеленого, оранжевого и от светло- до темно-коричневого различных оттенков в пределах этих цветов;
б) не допускаются посторонние включения, непропитанные участки, рваные кромки по длине ткани более 50 мм глубиной более 10 мм;
в) допускаются наплывы, подтеки, осыпание связующего в пределах, не выводящих показатель, массовая доля связующего из норм, указанных в табл.2, наплывы связующего на расстоянии до 150 мм от места соединения отдельных кусков ткани без проверки его содержания, дефекты внешнего вида, допускаемые на ленте или ткани.
(Измененная редакция, Изм. N 2).
1.5. По физико-механическим показателям материал должен соответствовать нормам, указанным в табл.2.
Таблица 2
Наименование показателя | Норма | Метод испытания
|
1. Массовая доля влаги и летучих веществ, %
| 2,6-6 | По п.4.11 |
2. Массовая доля связующего, %
| 33-40 | По п.4.12 |
3. Разрывная нагрузка неотвержденного образца по основе, Н (кгс), не менее
| 882 (90) | По п.4.14 |
4. Плотность, г/см | 1,4-1,7 | По ГОСТ 15139-69 и п.4.15 настоящего стандарта
|
5. Прочность при разрыве, МПа (кгс/см ), не менее
| 117 (1200) | По п.4.16 |
Примечания:
1. Допускается по согласованию с потребителем выпускать материал с массовой долей связующего 27-33%, при этом остальные нормы показателей должны соответствовать требованиям табл.2.
2. В течение гарантийного срока хранения материала допускается изменение массовой доли влаги и летучих веществ до 2%.
(Измененная редакция, Изм. N 1).
Пример условного обозначения материала П-5-7 ЛДП:
Материал П-5-7 ЛДП ГОСТ 17731-79
1.6. Таблица дополнительных показателей материала дана в справочном приложении.
1.7. Минимальный срок сохраняемости материала П-5-7 ЛДП - 30 сут со дня изготовления последней единицы продукции партии или части партии, а при хранении материала при температуре от плюс 5 до минус 20 °С - 60 сут.
(Введен дополнительно, Изм. N 1).
2. ТРЕБОВАНИЯ БЕЗОПАСНОСТИ
2.1. Работа должна проводиться в соответствии с санитарными правилами, утвержденными Министерством здравоохранения СССР. Помещения должны быть оборудованы приточно-вытяжной вентиляцией и противопожарными средствами.
2:2. Предельно допустимая концентрация пыли материала в воздухе рабочей зоны производственных помещений составляет 3 мг/м
.
При температуре 300-350 °С происходит деструкция материала с выделением фенола, альдегидов, аммиака, окиси углерода и др.
2.3. Работающие с материалом должны быть обеспечены спецодеждой и индивидуальными средствами защиты: халатами, перчатками, респираторами или марлевыми повязками.
2.4. По окончании работ необходимо принять теплый душ с мылом и смазать руки жировой смазкой.
3. ПРАВИЛА ПРИЕМКИ
3.1. Материал принимают партиями. Партией считают количество материала и единиц продукции, полученных на связующем, изготовленном на одной или смеси двух партий смолы одного предприятия-изготовителя и нескольких партиях кремнеземных наполнителей одной марки одного предприятия-изготовителя, сопровождаемое одним документом о качестве, содержащим:
наименование предприятия-изготовителя или его товарный знак,
наименование материала,
номер партии,
количество метров материала,
дату изготовления,
результаты проведенных испытаний и подтверждение о соответствии требованиям настоящего стандарта,
обозначение настоящего стандарта,
гарантийный срок хранения.
(Измененная редакция, Изм. N 1, 2).
3.2. Количество материала в партии должно быть: для ткани - не менее 700 м; для ленты - не менее 5000 м.
Допускается по соглашению с потребителем изменять количество продукции в партии.
Допускается поставка продукции частями, если количество материала в партии более 1400 м для ткани и 1000 м для ленты, при этом каждая часть партии принимается в соответствии с правилами приемки, установленными для партии.
Срок изготовления партии или части партии не должен быть более 7 сут с момента пропитки первой единицы продукции.
3.3. Контроль внешнего вида материала и показателей по подпунктам 1, 2 табл.2 изготовитель проводит на 100% продукции партии в процессе ее производства.
Контроль показателей по подпунктам 1, 2, 3 и 5 табл.2 проводят на 10% единиц продукции, но не менее двух, а по подпункту 4 табл.2 - на одной единице продукции.
3.4. При получении неудовлетворительных результатов испытаний хотя бы одного показателя повторный его контроль проводят на удвоенном количестве единиц продукции той же партии.
Результаты повторных испытаний распространяются на всю партию.
(Измененная редакция, Изм. N 1).
4. МЕТОДЫ ИСПЫТАНИЙ
4.1. Для проверки качества материала в виде ленты по подпунктам 1-5 табл.2 от наружного конца каждой контролируемой катушки отрезают не менее 10 м материала.
(Измененная редакция, Изм. N 1).
4.2. Для проверки качества по подпункту 1-3 табл.2 от наружного конца каждого контролируемого рулона материала в виде ткани отрезают 0,3 м материала полной ширины; по подпунктам 4, 5 - не менее 10 м материала шириной не менее 50 мм из любого места по ширине ткани, обрезав предварительно кромку шириной не менее 50 мм.
(Измененная редакция, Изм. N 1, 2).
4.3. Каждую пробу материала, отобранную по п.4.1 или п.4.2, упаковывают отдельно в мешок из полиэтиленовой пленки по ГОСТ 10354-82. В мешок вкладывают этикетку с указанием: наименования материала, номера партии, номера единицы продукции, даты отбора пробы и фамилии технического контролера, отобравшего пробу. Мешок заваривают или завязывают любым шпагатом.
4.4. Для проверки соответствия материала по подпунктам 1-2 табл.2 из любого места каждой пробы, отобранной по п.4.1 или п.4.2, вырезают по две заготовки площадью около 200 см
.
4.5. Для проверки соответствия материала по подпункту 3 табл.2 от каждой пробы, отобранной по п.4.1 или п.4.2, из любого места вырезают по пять полосок длиной (280±3) мм, шириной 40 мм. Полоски вырезают вдоль нитей основы. Образцы для испытаний изготовляют из полосок, выдергивая с обеих сторон крайние продольные нити основы с таким расчетом, чтобы ширина образца была доведена до (25±0,5) мм.
Ширину образца определяют как среднее арифметическое трех определений: в центре и на расстоянии около 50 мм от обоих концов образца. Крайние нити по длине образца с обеих сторон должны быть неповрежденными и не должны отделяться друг от друга.
Допускается вырезать полоски размером (280±3,0)
(25±0,5) мм с помощью шаблона, устанавливаемого продольной осью в направлении основы ткани.
(Измененная редакция, Изм. N 2).
4.6. Для проверки соответствия материала по подпунктам 4, 5 табл.2 из каждой пробы, отобранной по п.4.1 или п.4.2, изготовляют методом намотки не менее двух колец внутренним диаметром (100±0,5) мм, наружным диаметром (113±4) мм. Ширина колец должна быть равна ширине отобранной ленты.
Для лучшего уплотнения материала кольцо дополнительно обматывают пресс-материалом АГ-4С по ГОСТ 20437-75 или любым высокопрочным однонаправленным стеклопластиком, не уступающим по прочности на растяжение пресс-материалу АГ-4С, до наружного диаметра 112-120 мм. Режим изготовления кольца приведен в табл.3. Допускается при изготовлении колец пропускать ленту после разогрева через ролик, собирающий ленту в жгут. Каждое намотанное кольцо протачивают до толщины (3±0,2) мм и обрезают по краям на 5-7 мм. Полученное кольцо разрезают на кольца шириной (15±0,5) мм - для испытаний по подпункту 5 табл.2. Одно из колец шириной (15±0,5) мм разрезают на образцы размером (15±1)
(15±0,5)
(3±0,2) мм - для испытаний по подпункту 4 табл.2.
(Измененная редакция, Изм. N 1, 2).
Таблица 3
Параметр
| Норма |
1. Температура печи (длиной 350-400 мм) для разогрева материала П-5-7 ЛДП и АГ-4С, °С
| 150-350 |
2. Натяжение ленты материала П-5-7 ЛДП, кгс/см
| 7-12 |
3. Частота намотки, об/мин
| 7-20 |
4. Натяжение жгута пресс-материала АГ-4С шириной 8-12 мм, кгс
| 80-100 |
5. Температура в сушильном шкафу при загрузке колец на оправке, °С, не выше
| 40 |
6. Подъем температуры по циклам в сушильном шкафу, °С:
| |
1
| 115-125 |
2
| 135-145 |
3
| 155-170 |
7. Время подъема температуры по циклам, мин:
| |
1
| 40-50 |
2
| 10-20 |
3
| 10-20 |
8. Время выдержки при температуре по циклам, мин:
| |
1
| 115-125 |
2
| 115-125 |
3
| 115-125 |
9. Охлаждение колец на оправке в сушильном шкафу до температуры, °С
| 20-40 |
4.7. Образцы для определения плотности допускается вырезать из плит толщиной (10
) мм, изготовленных методом прямого горячего прессования открытым способом из пробы, отобранной по п.4.1 или п.4.2.
Режим изготовления плит приведен в табл.4.
Таблица 4
Параметр | Норма
|
1. Температура плит нагрева при запрессовке, °С
| 120
|
2. Время подъема температуры плит нагрева до температуры прессования, мин, не более
| 15 |
3. Температура прессования, °С
| 160
|
4. Удельное давление прессования, МПа (кгс/см )
| 4±1 (40±10)
|
5. Выдержка под давлением, мин
| 30±1 |
6. Охлаждение под давлением до температуры, °С, не выше | 100
|
7. Температура сушильного шкафа при загрузке плит, °С, не выше | 40
|
8. Средняя скорость подъема температуры в сушильном шкафу, °С/ч, не более
| 50 |
9. Выдержка в сушильном шкафу при 160 °С, ч
| 4-4,5
|
10. Охлаждение в сушильном шкафу до температуры, °С, не выше | 40
|
(Измененная редакция, Изм. N 1).
4.8. (Исключен, Изм. N 1)
4.9. Образцы для испытаний по подпунктам 4, 5 табл.2 должны иметь поверхность без вздутий и расслоений.
На образцах допускаются темные пятна, разнотонность окраски, поры.
4.10. Внешний вид материала определяют визуально при освещенности не менее 200 лк.
4.11. Определение массовой доли влаги и летучих веществ
4.11.1 Проведение испытания
Из каждой заготовки, изготовленной по п.4.4, вырезают один образец площадью около 100 см
, взвешивают с погрешностью не более 0,001 г и выдерживают в сушильном шкафу при температуре (130±5) °С в течение 10 мин. Затем образцы охлаждают в эксикаторе до комнатной температуры и снова взвешивают с той же погрешностью.
4.11.2. Обработка результатов
Массовую долю влаги и летучих веществ (
) в процентах вычисляют по формуле
,
где
- масса образца до сушки, г;
- масса образца после сушки, г.
4.12. Определение массовой доли связующего
4.12.1. Проведение испытания
Образцы после определения массовой доли влаги и летучих веществ помещают в нагретую до температуры 800-900 °С муфельную печь на огнеупорные подставки (тигли) и выдерживают их в течение 10-20 мин до полного выгорания связующего (до белого цвета). Затем образцы охлаждают в течение 1-2 мин на воздухе, потом в эксикаторе до комнатной температуры и взвешивают с погрешностью не более 0,001 г.
4.12.2. Обработка результатов
Массовую долю связующего (
) в процентах вычисляют по формуле
,
где
- масса образца после сушки, г;
- масса образца после выжигания, г.
4.13. За результат испытаний по пп.4.11, 4.12 принимают среднее арифметическое двух определений, вычисленное с погрешностью не более 0,01%. При этом значение каждого определения должно соответствовать нормам, указанным в подпунктах 1, 2 табл.2. Если значение одного из определений не соответствует нормам табл.2, то проводят третье определение на образце, вырезанном из той же пробы.
За результат испытаний принимают среднее арифметическое двух определений, соответствующих нормам, указанным в подпунктах 1, 2 табл.2.
В документ записывают результаты испытаний всех контролируемых единиц продукции, округленные до 0,1%.
4.14. Разрывную нагрузку неотвержденного образца по основе определяют на пяти образцах, изготовленных по п.4.5.
Испытания проводят в атмосфере окружающей среды. Продолжительность выдержки образцов при этих условиях перед испытанием должна быть не менее 1 ч.
Испытание проводят на любой испытательной машине с самоцентрирующими зажимами, позволяющей производить измерение нагрузки с погрешностью, не превышающей 1% от величины измеряемой нагрузки. Зажимы машины должны обеспечивать надежное крепление образца и совпадение его продольной оси с направлением растяжения.
Скорость движения подвижного захвата испытательной машины должна быть (100±5) мм/мин.
При испытании образец закрепляют так, чтобы расстояние между зажимами составляло (100±2) мм.
За результат испытаний принимают максимальное значение разрывной нагрузки каждого образца, определяемой по шкале силоизмерительного механизма испытательной машины.
За величину разрывной нагрузки каждой контролируемой единицы продукции принимают среднее арифметическое значение из пяти определений, округленное до 1,0 Н (0,1 кгс).
В документ записывают величины разрывной нагрузки всех контролируемых единиц продукции, округленные до целого числа.
При разногласиях, возникших при оценке разрывной нагрузки неотвержденного образца по основе, определение проводят на полоске, вырезанной по п.4.5 без применения шаблона.
(Измененная редакция, Изм. N 2).
4.15. Плотность определяют по ГОСТ 15139-69 методом гидростатического взвешивания при температуре (20±5) °С на трех образцах размером (10
)
(15±0,5)
(12-15) мм или (15±1)
(15±0,5)
(3±0,2) мм. Образцы перед испытанием должны находиться при указанной температуре не менее 1 ч.
За результат испытаний принимают среднее арифметическое всех определений.
В документ записывают результат, округленный до 0,1 г/см
.
Допускается определять плотность по ГОСТ 15139-69 методом обмера и взвешивания пяти колец, предназначенных для определения прочности при разрыве.
При разногласиях, возникших при оценке плотности, определение проводят методом гидростатического взвешивания.
(Измененная редакция, Изм. N 1, 2).
4.16. Прочность при разрыве определяют на пяти кольцах, изготовленных по п.4.6 от каждой отобранной единицы продукции, с внутренним диаметром (100,0±0,5) мм, шириной (15,0±0,5) мм, толщиной (3,0±0,2) мм.
Перед испытанием образцы выдерживают не менее 1 ч в условиях окружающей среды и измеряют их ширину и толщину в трех точках, равномерно расположенных по периметру с погрешностью не более 0,05 мм.
За результат измерения принимают среднее арифметическое трех определений.
Испытание проводят на любой испытательной машине, оснащенной приспособлением, приведенным на чертеже, и позволяющей измерять нагрузки с погрешностью, не превышающей 1%.
Рис. Приспособление и образец для испытания на растяжение
Приспособление и образец для испытания на растяжение
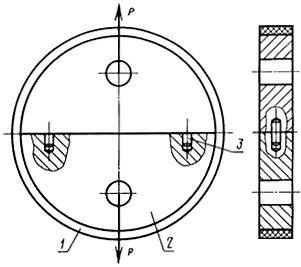
1 - образец; 2 - полудиск; 3 - штифт
Испытание ведут с постепенным увеличением нагрузки до разрушения образца. Скорость движения подвижного захвата машины должна быть 10-20 мм/мин. Испытание проводят в условиях окружающей среды.
Предел прочности при растяжении (
) в МПа (кгс/см
) вычисляют по формуле
,
где
- разрушающее усилие, Н (кгс);
- площадь поперечного сечения кольцевого образца, м
(см
);
1,28 - коэффициент, учитывающий снижение разрушающего напряжения в результате изгиба в месте разрушения.
За результат испытаний принимают среднее арифметическое из пяти определений, вычисленное с погрешностью не более 0,1 МПа (1,0 кгс/см
).
В документ записывают результаты испытаний всех контролируемых единиц продукции.
(Измененная редакция, Изм. N 1).
5. УПАКОВКА, МАРКИРОВКА, ТРАНСПОРТИРОВАНИЕ И ХРАНЕНИЕ
5.1. Материал, намотанный на фанерные или дюралевые катушки, должен быть упакован в двойные мешки из полиэтиленовой пленки по ГОСТ 10354-82, а затем в мешочную бумагу по ГОСТ 2228-81 и завязан любым шпагатом или склеен липкой лентой на бумажной или полиэтиленовой основе.
Материал в рулоне, плотно намотанный на бумажно-бакелитовые или поливинилхлоридные гильзы диаметром 75-80 мм, длиной (1000±100) мм, должен быть упакован в полиэтиленовую пленку не менее чем в два слоя. Свободные концы пленки плотно завязывают любым шпагатом. Затем рулон обертывают мешочной бумагой и снова завязывают шпагатом или склеивают липкой лентой.
Смещение краев ткани относительно друг друга не должно быть более 30 мм на одном торце рулона; другой торец рулона не контролируется.
При использовании материала на предприятии-изготовителе допускается упаковывать его одним слоем полиэтиленовой пленки и смещение краев ткани в рулоне более чем на 30 мм, если предусмотрена разрезка его на ленты при одновременной перемотке и контроле положения кромки ленты.
Допускается разница толщины намотки материала на гильзе до 25 мм.
По согласованию с потребителем допускается использование других видов гильз.
Диаметр отверстия катушки согласовывается между изготовителем и потребителем.
(Измененная редакция, Изм. N 2).
5.2. К каждой катушке или рулону приклеивают этикетку с указанием:
а) наименования предприятия-изготовителя или его товарного знака;
б) наименования материала;
в) количества метров;
г) номера партии;
д) номера единицы продукции;
е) массовой доли влаги и летучих веществ и связующего;
ж) даты изготовления;
з) обозначения настоящего стандарта;
и) фамилии аппаратчика.
5.3. Материал в рулоне, упакованный по п.5.1, укладывают в деревянные ящики со специально оборудованным приспособлением для закрепления рулонов, предохраняющим материал отслеживания и перемещений. Катушки с материалом, упакованные по п.5.1, укладывают в любые деревянные ящики по требованию потребителя так, чтобы не было перемещения.
5.4. Транспортную тару маркируют по ГОСТ 14192-96 с указанием:
а) наименования предприятия-изготовителя или его товарного знака;
б) наименования материала;
в) номера партии;
е) количества метров материала;
ж) даты изготовления;
з) фамилии упаковщика;
и) обозначения настоящего стандарта.
Ящик, в который вкладывается документ, дополнительно маркируют "Документ здесь".
(Измененная редакция, Изм. N 2).
5.5. (Исключен, Изм. N 1).
5.6. Материал, упакованный по п.5.3, транспортируют в крытых транспортных средствах при температуре окружающей среды. При внутризаводском транспортировании допускается перевозка материала без дополнительной упаковки в ящики.
Пакетирование материала производят по НД. Средства скрепления - по ГОСТ 21650-76. Материал допускается транспортировать в универсальных контейнерах и в непакетированном виде.
(Измененная редакция, Изм. N 2).
5.7. Материал в рулоне должен храниться в упаковке, предусмотренной п.5.1, в складских помещениях при температуре не выше 25 °С на стойках, предохраняющих его от слеживания. Материал в рулоне опирается на стойки свободными концами гильз. Катушки с материалом, упакованные по п.5.1, должны храниться на стеллажах или решетках в складских помещениях при температуре не выше 25 °С.
Расстояние от пола до стеллажа или решетки - не менее 10 см по высоте. В течение 10 сут хранения материала допускается повышение температуры в помещении до 35 °С.
6. ГАРАНТИИ ИЗГОТОВИТЕЛЯ
6.1. Изготовитель гарантирует соответствие материала П-5-7 ЛДП требованиям настоящего стандарта при соблюдении условий транспортирования и хранения.
(Измененная редакция, Изм. N 1).
6.2. Гарантийный срок хранения материала - 30 сут со дня изготовления последней единицы продукции партии или части партии.
При хранении материала при температуре от плюс 5 до минус 20 °С гарантийный срок хранения - 60 сут.
6.3. (Исключен, Изм. N 1).
7. УКАЗАНИЯ ПО ПРИМЕНЕНИЮ
По истечении минимального срока сохраняемости материал перед применением следует проверить на соответствие требованиям настоящего стандарта.
(Введен дополнительно, Изм. N 1).
ПРИЛОЖЕНИЕ (справочное). ТАБЛИЦА ДОПОЛНИТЕЛЬНЫХ ПОКАЗАТЕЛЕЙ МАТЕРИАЛА
ПРИЛОЖЕНИЕ
Справочное
Наименование показателя | Норма
|
1. Относительная массовая доля растворимой части связующего, %, не менее
| 90 |
2. Водопоглощение за 24 ч, %, не более
| 3,5 |
3. Предел прочности при скалывании, МПа (кгс/см ), не менее
| 8,8 (90) |
4. Коэффициент теплопроводности, Вт/м·°С, при температуре, °С:
| |
25
| 0,41-0,45 |
100
| 0,43-0,46 |
200
| 0,45-0,50 |
250
| 0,47-0,49 |
300
| 0,46-0,49 |
5. Коэффициент температуропроводности, 10 ·м /с, при температуре, °С:
| |
25
| 0,29-0,32 |
100
| 0,21-0,24 |
200
| 0,19-0,23 |
250
| 0,22-0,27 |
300
| 0,26-0,33 |
6. Коэффициент линейного теплового расширения, 10 ·1/°С, в интервале температур, °С:
| |
от минус 60 до 0
| 4,8-5,4 |
0 до 50
| 5,3-5,7 |
50 " 100
| 2,1-5,2 |
100 " 150
| 2,1-4,1 |
150 " 200
| 0,4-3,3 |
7. Линейная плотность, кг/м (для ткани)
| Приблизительно 0,4 |